Have you ever wondered how something as simple as Hydroxypropyl Methylcellulose (HPMC) can have such a profound impact on industries like construction, coatings, or pharmaceuticals? What if poor quality control led to cracks in your building’s walls or peeling paint? Imagine the cost of rework or loss of reputation. Quality control in HPMC production isn’t just a precaution—it’s a necessity.
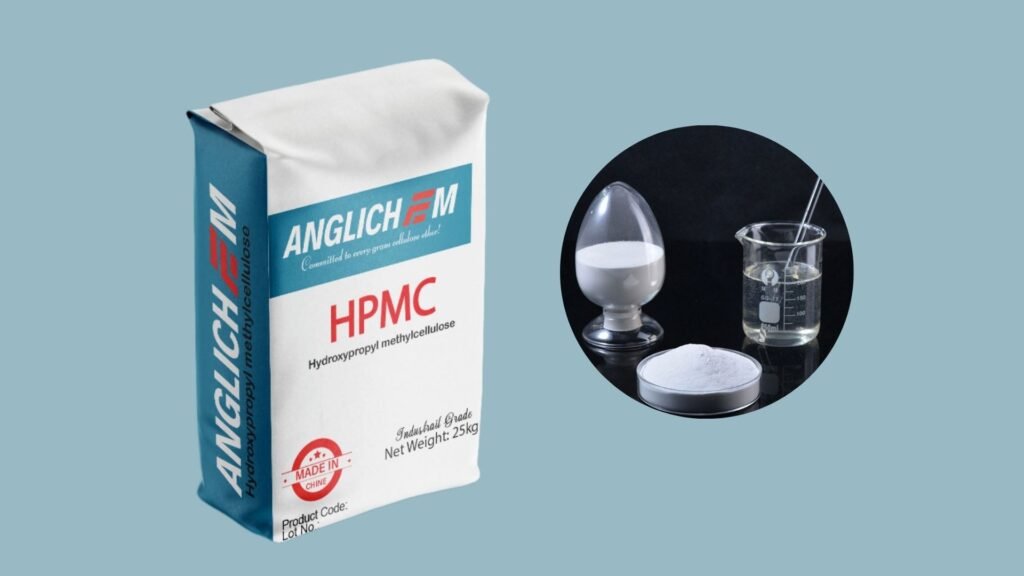
In this article, I’ll share why quality control is crucial for industrial-grade HPMC, how it affects your products, and what steps you should take to ensure you’re getting the best.
To put it simply, without stringent quality control, even the best HPMC can fail to meet its intended purpose. As a decision-maker in your industry, ensuring that your HPMC supplier follows rigorous quality standards is the first step toward achieving reliability, durability, and performance in your products.
But what does quality control actually involve when it comes to HPMC? How can you be sure the product you receive is consistent, safe, and effective for your applications? Let’s dive into the process.
What is Industrial-Grade HPMC?
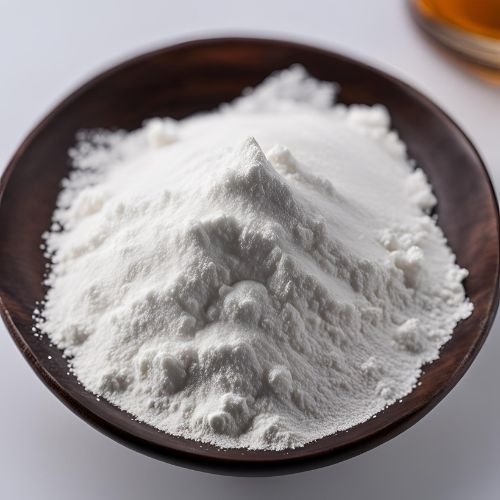
As you may already know, HPMC is a cellulose ether that plays an essential role across multiple industries. From construction materials like mortars and adhesives to pharmaceutical and food applications, its versatility is unmatched.
But what makes industrial-grade HPMC so special? Unlike food-grade or pharmaceutical-grade HPMC, industrial-grade HPMC is specifically designed to meet the high demands of construction and other heavy industries. Whether it’s enhancing the adhesion of adhesives or improving the viscosity in coatings, its performance is crucial for the longevity of your products.
Why Does Quality Control Matter for HPMC?
In industries like construction and chemical manufacturing, using subpar HPMC can lead to disastrous results. Imagine the adhesive in your tile setting mortar failing under pressure, or a wall plaster losing its strength because the HPMC didn’t maintain its expected viscosity. These failures aren’t just minor inconveniences—they can lead to costly repairs and damage to your reputation.
Effective quality control ensures that every batch of HPMC you receive performs as expected—whether in self-leveling compounds, adhesives, or dry mixes.
How is Quality Controlled in HPMC Production?
Ensuring high-quality HPMC involves several critical steps, and as someone deeply involved in sourcing these materials, I can tell you that quality control begins from the very start.
Step 1: Sourcing High-Quality Raw Materials
The first step is sourcing high-quality cellulose fibers and chemical reagents. The quality of raw materials directly influences the final product’s consistency. A reputable supplier will ensure these raw materials meet industry standards, forming the foundation of quality HPMC.
Step 2: In-Process Monitoring
Once production begins, continuous monitoring is essential. Key parameters like viscosity, moisture content, and particle size must be measured regularly. This is critical to avoid deviations that can impact the final performance of the product. In the construction industry, for instance, low viscosity can result in poor adhesion in mortar or tile adhesive applications.
Step 3: Final Batch Testing
Before HPMC is shipped, every batch undergoes a series of tests. These tests evaluate solubility, chemical composition, and impurity levels to ensure the final product meets the required specifications. The goal is to prevent any issues from slipping through the cracks and affecting the quality of the finished product.
What are the Best Practices for Ensuring High-Quality HPMC?
In my 20+ years of working with HPMC, I’ve seen firsthand the importance of implementing best practices for ensuring product quality. Here’s what I recommend:
- Supplier Transparency: The best way to ensure you’re getting high-quality HPMC is to work with a supplier who is open about their processes. Ask for test results, certifications, and reports. A transparent supplier will provide documentation of the tests they’ve conducted, which helps you make informed decisions.
- Regular Audits and Testing: Choose suppliers who invest in regular audits of their production process. Batch testing and quality audits should be part of the process, not just an afterthought.
- Long-Term Relationships: Building a long-term relationship with a trusted supplier can ensure consistent quality over time. A reliable supplier will understand your requirements and work closely with you to meet your needs.
What Certifications Should You Look for in Your HPMC Supplier?
When you’re sourcing industrial-grade HPMC, always check for certifications that guarantee quality. For example:
- ISO 9001 certification indicates that the supplier adheres to international standards for quality management. It assures that the supplier’s processes are efficient, reliable, and consistently produce high-quality products.
- GMP (Good Manufacturing Practice) certification is especially important if you’re using HPMC in pharmaceutical or food applications. It ensures that the supplier follows strict health and safety regulations, which is critical for end-product safety.
- Other relevant industry certifications,Depending on the specific application area, other specific certifications may be required, such as CE certification, RoHS certification, etc., to ensure that the product meets the regulatory requirements of the specific market.
These certifications are your guarantee that the supplier’s quality control measures meet global standards, and that you’re receiving a product you can trust.
Rigorous testing ensures product consistency and performance, particularly when used in critical applications like construction and pharmaceuticals.
Conclusion
At the end of the day, the quality of HPMC you use directly affects the performance and durability of your final products. Whether you’re working in construction, tile adhesives, or self-leveling compounds, ensuring the quality of your HPMC will help you avoid costly errors and rework.
By focusing on supplier transparency, certifications, and continuous testing, you can ensure that your HPMC is of the highest quality. Don’t cut corners—invest in quality control, and it will pay off in the long run.